Rules and Regulations for Well-Drillers, Pump Installers, and Water Filtration Contractors
440-RICR-10-00-6 ACTIVE RULE
6.1Authority
These rules and regulations are promulgated by the Contractors’ Registration and Licensing Board (Board) in accordance with R.I. Gen. Laws §§ 5-65-17 and 5-65.2.
6.2Purpose
The purpose of this Part is to administer and enforce the provisions of the Rhode Island Well Drilling, Pump Installers, and Water Filtration Contractors Law, R. I. Gen. Laws Chapter 5-65.2, to establish a licensing program and minimum standards for governing and enforcing the installation, construction, repair, development, and abandonment of wells, well pumps, water-supply systems, water-treatment systems, and water-filtration systems to ensure competency in the field and to safeguard the public health and to provide an adequate supply of clean and uncontaminated water for all persons in the state. Any person who fails to license as a well-driller, pump installer, or water filtration contractors, as stipulated, is subject to penalties for operating without a license.
6.3Incorporated Materials
Reserved
6.4.Definitions
6.4.1General Definitions
A.In addition to the terms defined in R.I. Gen. Laws §§ 5-65-1, 5-65.2-2, and § 1.4 of this Subchapter, for the purpose of this Part, the following terms shall have the following meanings:
1.“Abandoned Well” means a well, test well, or borehole that has gone dry, is contaminated, or no longer serves a useful purpose.
2.“Access port” means a minimum 3/4 inch tapped hole and plug, or a 3/4-inch pipe welded onto the casing in the upper portion of a well casing to permit entry of water-level measuring devices into the well.
3.“Adequate protection” means construction methods which assure protection of ambient groundwater from the introduction of contamination.
4.“Air line” means a water level measuring device consisting of a pressure gauge attached to an airtight line or pipe within the well bore extending from land surface to below the pumping level measuring the stable air pressure remaining in the line after completely purging water from within the line.
5.“Alter” means the replacing or repairing of any portion of an existing water supply system and the terms "alteration" and "altering" shall be construed accordingly.
6.“Altering a well” means the deepening, hydro-fracturing, reaming, casing, re-casing, perforation, re-perforating, and installation of liner pipe, packers, seals, and any other material change in the design or construction of a well.
7.“Annular space” means the space between two objects, one of which is surrounded by the other. This includes the space between the wall of an excavation and the wall of a pit; between the wall of an excavation and the casing of a well; or between two casings.
8.“Aquifer” means a geologic formation, group of formations, or part of a formation that contains saturated and permeable material capable of transmitting water in sufficient quantity to supply wells or springs. The terms water-bearing zone or water-bearing stratum are synonymous with the term aquifer.
9.“Artesian sell” means a well in which groundwater is under sufficient head to rise above the level at which it was first encountered whether the water flows at land surface. If the water level stands above land surface, the well is a flowing artesian well.
10.“Bentonite clay grout” means a mixture of bentonite clay and water.
11.“Bored well” means a well, constructed with the use of earth augers turned either by hand or by power equipment.
12.“Buried slab type well” means a dug well in which well casing is used to case the upper hole. A slab, sealed with cement grout, is placed between the upper hole and lower drill hole, and the remainder of the annulus is filled with concrete.
13.“Casing” means the tubing, pipe, or conduit, installed in the borehole during or after drilling. The term "casing" does not include slotted or perforated pipe, well screens, or liner pipe.
14.“Casing seal” means the watertight seal established in the well bore between the well casing and the drill hole wall to prevent the inflow and movement of surface water or shallow ground water in the well annulus, or to prevent the outflow or movement of water under artesian or hydrostatic pressures.
15.“Cement grout” means a mixture of cement, sand, and water.
16.“Cesspool” means a covered pit with open jointed lining for the reception of untreated sewage, the liquid portion of which is disposed of by seepage or leaching into the surrounding soil and the solids or sludge being retained in the pit.
17.Cistern” means a tank for the reception of rain water, intended for non-potable water supply system.
18.“Clay” means a fine-grained, inorganic material having plastic properties and with a predominant grain size of less than 0.005 mm.
19.“Commercial water-filtration/treatment-system work” means any alteration, installation or repair of water-filtration/treatment systems in which the piping exceeds one and one-half inches (1.5") or the flow rate exceeds eighty (80) gallons per minute.
20.“Confining formation” means the "impermeable" stratum immediately overlying an artesian (confined) aquifer.
21.“Consolidated formation” means materials that have become firm through natural rock-forming processes. It includes such materials as basalt, sandstone, hard claystone, conglomerate, and granite.
22.“Construct” means to build, assemble, or install a new water supply system, water treatment system, or the enlargement or alteration of an existing water supply system.
23.“Contamination” means the presence of sewage, industrial wastes, organisms of the coliform group, or harmful or objectionable material which is in, or may gain access to, potable water.
24.“Decommission” means the act of completely filling a well, test well or bore with sealant from the original depth to the surface, in accordance with this Part, so that it is no longer a conduit to the aquifer.
25.“Disinfection” means the inactivation of harmful organisms presents in water.
26.“Disposal field” means an area consisting of disposal trenches, a disposal bed, or a combination thereof used for dispersion of the liquid portion of sanitary sewage into the ground as close to the surface as feasible.
27.“Disposal trench” means a shallow ditch with vertical sides and flat bottom partially filled with a satisfactory filtering material in which a single distribution line has been laid, covered with top soil and suitable vegetation.
28.“Distribution box” means a watertight structure which receives sanitary sewage effluent from a septic tank and distributes such sewage effluent to two or more pipelines leading to a disposal field.
29.“Distribution lines” means a series of open-jointed or perforated pipes used for dispersion of sewage into a disposal field.
30.“Distribution main” means the pipe for the transmission or conveyance of potable water to more than one structure.
31.“Domestic well” means a well that supplies water to a water supply system for drinking, culinary, or household uses, and which is not used as a public water supply.
32.“Drawdown” means the difference in vertical distance between the pumping level and the static water level in a well or the area outside of the well.
33.“Driven well” means a well, constructed by driving into the ground a well-point fitted to the end of a pipe section or series of pipe sections.
34.“Dry well” means a covered pit with open-jointed lining through which drainage from roofs, basement floors or area-ways may seep or leach into the surrounding soil.
35.“Dug well” means a well in which the excavation is made using picks, shovels, spades, or digging equipment, such as backhoes, clam shell buckets, or sand bucket.
36."Electrical work" means the limited electrical installation, connection, and services from a drop/wall switch, as supplied by a properly licensed electrician for water-supply systems, water-filtration systems, water-treatment systems, and pump installations. Contractors, as defined herein, may perform this limited electrical work. This definition shall not exclude or prevent any properly licensed electrician from performing this work.
37.“Emergency work” means an unexpected event which affects the residents’ health, safety, and welfare, which must be corrected or rectified on an immediate need basis. In such instance, the contractor shall within 72 hours of completion of work, have the owner or owner’s representative sign an invoice/contract noting the scope of work and the amount of charges as well as obtain any required permits.
38.“Established ground surface” means the permanent elevation of the surface of the ground at the site of the well after completion of grading, excavation; or other land movement.
39.“Filtration system” means water treatment system.
40.“First draw” means a sample from a filter-free, cold water tap that is routinely used for consumption and with a minimum six (6) hour stagnation time.
41.“Gravel packed well” means a well in which the area immediately surrounding the well screen or perforated pipe within the water-producing zone is filled with graded coarser material.
42.“Groundwater” means water encountered below the ground surface of the earth within the zone of saturation that can supply wells and springs.
43.“Grout” means a supple, impervious bonding material which can provide a water tight seal between the casing and the formation throughout the depth required protecting against objectionable matter, and which is essentially free of shrinkage. This shall include but not be limited to neat cement grout, sand clay, bentonite cement grout.
44.“Grout Pipe” means the same as "Tremie Pipe"
45.“Hydraulic conductivity” means the ability of material to transmit fluid, usually described in units of gallons per day per square foot of cross-section area. It is related to the effectiveness with which pore spaces transmit fluids.
46.“Hydro fracturing” means a procedure whereby high-pressure water injection is used in an attempt to fracture or widen existing fractures or propagate limited fractures in a water bearing to increase a well's productivity.
47.“Industrial waste” means liquid or solid waste resulting from the processes employed in industrial establishments.
48.“Jaswell seal” means a type of seal that seals off a portion of the well hole. The Jaswell can seal off just the level of concern or can seal off the entire area from the top to the concern area.
49.“Jetted well” means a well in which the excavation is made using a high velocity jet of water.
50.“Leakage” means leakage of surface and/or subsurface water around the well casing.
51.“Limited plumbing” means the required cutting of a water service/supply pipe, for the purpose of installing a supply and return to connect water-filtration/treatment system, pump equipment and also includes drainage for point of use equipment. Any repair, or re-piping of the water service/supply pipe, to bypass an outdoor faucet, irrigation system, etc., shall be considered “Plumbing Work” which may only be performed by a R.I. Licensed Plumber.
52.“Liner pipe” means pipe that is installed inside a completed and cased well for the purpose of sealing off undesirable water or for repairing ruptured or punctured casing or screens.
53.“Locate” means the designation of the site or place of the sources or other appurtenances of a water supply system, and the term “location” shall be construed accordingly.
54.“Lower drill hole” means that part of the well bore extending below the surface seal interval in a well.
55.“Mineralized water” means any naturally occurring ground water containing an amount of dissolved chemical constituents limiting the beneficial uses to which the water may be applied.
56.“Neat cement grout” means a mixture of not more than six gallons of clear water to one bag of cement.
57.“Non–community water system” means a public water system that is not a community water system. A non-community water system is either a “transient non-community water system (TNC)” or a “non- transient non-community water system (NTNC).
58.“Onsite wastewater treatment system” or “OWTS” means any system of piping, tanks, dispersal areas, alternative toilets or other facilities designed to function as a unit to convey, store, treat or disperse wastewater by means other than discharge into a public wastewater system.
59.“Oversized drill hole” means an excavation which is larger than the outside diameter of the well casing, constructed for the emplacement of a well.
60.“Perched ground water” means ground water held above the regional or main water table by a less permeable underlying earth or rock material.
61.“Petcock valve” means a valve used to contain pressure and when opened, to drain the line or pipe.
62.“Pitless adaptor” means a device fabricated at the job site designed for attachment to one or more openings through a well casing, and so constructed as to prevent the entry of contamination into the well or potable water, conduct water from the well, prevent the water from freezing or extremes of temperature, and provide access to water system components within the well.
63.“pH” means the measurement of the acidity in water.
64.“Point-of-entry treatment” means water treatment that serves the entire house by treating water and reducing contaminants as it enters the structure.
65.“Porosity” means the ratio of the volume of voids in the geologic formation being drilled to the overall volume of the material without regards to size, shape, inter-connection, or arrangement of openings.
66.“Potability” means the determination that water is potable and is safe for consumption.
67.“Potable water” means water that meets human consumption standards of the R.I. Department of Health or the U.S. Environmental Protection Agency, whichever is more restrictive.
68.“Potentiometric surface” means the level to which water will rise in tightly cased wells.
69.“Pressure grouting” means a process by which a cement grout is confined within the drill hole or casing by the use of retain plugs or packer and by which sufficient pressure applied to drive the grout slurry into the annular space or zone to be grouted.
70.“Private water system” means a system that extracts groundwater from a well or well field (wells on one (1) or more properties), provides potable water for human consumption, and does not meet the requirements to be classified as a public water system. These systems also include commercial – mixed use, multi-family residential, single/duplex residential, and individual private systems.
71.“Private well” means a water well that can serve as a private drinking water system.
72.“Private well water testing report form” means a standardized form for the reporting of certified laboratory results to be disseminated to the well owner or client to determine if the water is potable.
73.“Public health hazard” means a condition whereby there are sufficient types and amounts of biological, chemical, or physical, including radiological, agents in relation to water which are likely to cause human illness, disorders, or disability. These include, but are not limited to pathogenic viruses, bacteria, toxic chemicals, and radioactive isotopes.
75.“Public water system” means a system for the provision to the public of water for human consumption through pipes or constructed conveyances; if such a system has at least fifteen (15) service connections or regularly serves at least twenty-five (25) individuals daily at least sixty (60) days out of the year.
76.“Pump” means mechanical equipment or device used to move, raise, compress, or transfer water.
77.“Pump installation” means the industry, procedure, and all operations engaged in by any person, full-time or part-time, for compensation or otherwise, to connect a pump or pipe to a water system or its appurtenances, or to install a pump or pipe in a well and the procedures for licensing well drillers and pump installers.
78.“Pump test” means the procedure involving pumping water for a specified period to determine the yield characteristics of a well.
79.“Pumping level” means the level of the water surface in a well while it is being pumped or bailed.
80.“Repair” means any work involved in the reaming, sealing, installing, changing of casing depths, perforating, screening, cleaning, acidizing, or other redevelopment of a well, pump or filtration system.
81.“Rough drilling log” means a record kept on the well site of the information needed to complete the well report for the well being constructed.
82.“Sand” means a detrital material having a prevalent grain ranging from 2 millimeters to 0.06 millimeters.
83.“Sand clay or bentonite cement grout” means a mixture of one-part fine sand, one-part clay or bentonite, and one-part cement and five to six gallons of water for every hundred pounds of the mixture.
84.“Sand cement grout” means a mixture of not more than two parts sands to one-part cement, and not more than six gallons of clear water to each bag of cement.
85.“Sanitary sewage” means any liquid waste containing animal or vegetable matter in suspension or solution, or the water-carried wastes resulting from the discharge of water closets, urinals, laundry tubs, washing machines, sinks, dishwashers, or any other source of water-carried waste of human origin or containing putrescible material.
86.“Sanitary sewer” means a pipe which carries sewage and to which storm, surface, and groundwater waters are not intentionally admitted.
87.“Seepage pit” means a covered pit with open-jointed lining material which septic or laundry waste may seep or leach into surrounding soil.
88.“Septic tank” means watertight receptacle which receives the discharge of sanitary sewage and is designed and constructed to permit settling of settleable solids from the liquid, digestion of the organic matter by detention, and discharge of the liquid portion into a disposal field.
89.“Service line” means a pipe for the transmission or conveyance of potable water under pressure either from an individual well or from a distribution main, to a realty improvement.
90.“Shared well” means a common well or well field that provides drinking water to more than one (1) residential unit, commercial enterprise, or any combination that does not meet the definition of public well.
91.“Silt” means unconsolidated elastic sediment composed predominantly of particles between 0.06 and 0.005 millimeters in diameter.
92.“Specific capacity” means the yield of a well expressed in gallons per minute per foot of drawdown, as abbreviated gpm/ft.
93.“Spring” means a natural surface feature where groundwater issues from the rock or soil onto the land or into a body of water.
94.“Static water level” means the depth to the surface of the water in a well measured from the land surface or other convenient, permanent, and specified datum, when no water is being discharged from the well and the water level has reached equilibrium.
95.“Stratum” means a bed or layer of a formation that consists throughout of approximately the same type of consolidated or unconsolidated material.
96.“Subsurface sewage disposal system” means an individual sewage disposal system.
97.“Suction line” means a pipe that conveys water at less than atmospheric pressure from a well to a pump.
98.“Sump” means a hole dug to a depth of ten feet or less with a diameter greater than ten feet in which water is sought or encountered.
99.“Supervision” means the physical presence of a licensee during all work of well-drilling, pump installation, and water-filtration/treatment, including repairs and service.
100.“Surface water” means the water found on the ground surface or contained in a stream, pond, lake, wetland, or other natural watercourse.
101.“Surging” means the use of a solid plunger in an up and down plunging motion to increase well productivity by forcing water into and out of existing fissures.
102.“Temporary removal from service” means to remove a drilling machine from a well site prior to putting the well into service or returning it to service or subsequent to completing or altering a well, or to remove a well form service with the intent of using it in the future.
103.“Test well” means a temporary well installed to obtain data.
104.“Transient non-community water system” or “TNC” means a non-community water system that does not regularly serve at least twenty-five (25) of the same persons over six (6) months per year.
105.“Tremie pipe” means a pipe which is used to place grout at the bottom of the sealing interval of a well.
106.“Unconsolidated formation” means naturally occurring loosely cemented or poorly indurated materials including clay, sand, silt, and gravel.
107.Undersized hole” means an excavation which is no larger than the internal diameter of the well casing, constructed for the emplacement of a well.
108.“Upper drill hole” means that part of the well bore extending from land surface to the bottom of the surface seal interval.
109.“Water authority” means an entity supplying water and regulated by the Rhode Island Department of Health.
110.“Water bearing formation” means aquifer.
111.“Water table well” means the upper surface of an unconfined water body, the surface of which is at atmospheric pressure and fluctuates seasonally. The water table is defined by the levels at which water stands in wells that penetrate the water body.
112.“Water treatment system” means any apparatus for treating, filtering, or processing water to modify, enhance, or improve its quality or to meet a specific water quality need, desire, or standard in the pipes, fittings, and other components servicing such apparatus.
113.“Well cap” means a watertight sanitary device that covers and encloses the upper termination of a pitless well unit or the well casing and provides watertight connections for electrical power lines and well vents.
114.“Well drilled” means a well, constructed by drilling a hole and inserting a casing to support the sides of the hole.
115.“Well drilling machine” means any power-driven percussion, rotary, boring, digging, or auguring machine used in the construction or alteration of wells.
116.“Well, dug” means a well excavated into a shallow aquifer.
117.“Well, geothermal” means a well that is drilled; bored, augured, or dug to allow piping to be installed to utilize the earth’s temperature for heating or cooling purposes.
118.“Well, irrigation” wells of all types of construction for the sole use of irrigation.
119.“Well, monitoring” means a well that is specifically located, designed, constructed, and emplaced to sample groundwater quality and/or measure water table elevations.
120.“Well seal” means an approved arrangement or device used to cap a well or to establish and maintain a junction between the casing and curbing of a well and the pipe or equipment installed therein, the purpose or function of which is to prevent contaminants from entering a well at the upper terminal.
121.“Well unit” a pre-assembled device which extends the upper end of a well casing to above grade, provided with a pitless well cap, and so constructed as to prevent the entry of contamination into the well or potable water, conduct water from the well, protect the water from freezing or extremes of temperature, and provide access to the well and to the water system components within the well.
122.“Well vent” means an outlet at the upper terminal of a well casing to allow equalization of air pressure in a well but at the same time so constructed as to avoid entry of water and foreign material into the well.
123.“Well yield” means the quantity of water per unit of time which may flow or be pumped continuously from a well.
6.4.2Private Water System Classifications:
A.Commercial/Mixed Use Private Water Systems include, but are not limited to, small multi-unit commercial spaces or mixed-use (commercial/residential) buildings. This type of system provides potable water to tenants as part of some form of rental or lease agreement entered into by the owner of the system as part of a commercial enterprise.
B.Multi-Family Residential/Shared Well Private Water System designed to supply multiple residential units with potable water. These systems may include but are not limited to; small apartment buildings or multiple houses/condominiums on a shared well or private well field.
C.Single/Duplex Residential Private Water System are designed to supply one or two tenants of record with potable water for consumption and use. The residential units (up to 2) associated with this type of system are not owner occupied.
D.Individual Private Water Systems are designed to supply an owner(s) and/or one tenant of record with potable water for consumption and not meeting the definition of a public water system.
6.5General Administration and Procedures
A.Administrative procedures for the licensing of well-drillers, pump installers, water filtration contractors, and water filtration installers shall comply with R.I. Gen. Laws Chapters 5-65, 5-65.2 and the following sections of Part 1 of this Subchapter:
1.Delivery of Notices: § 1.5(A) of this Subchapter.
2.Change of Address § 1.5(B) of this Subchapter
3.Public Records and Information Requests: § 1.5(C) of this Subchapter.
4.Certification of Registration/License § 1.5(D) of this Subchapter.
5.Filing Fees and Record Changes § 1.5(E) of this Subchapter.
B.Requirement for Written Contract
1.All well drilling, pump installing, and/or water filtration work, including the cost of labor and materials, in excess of one thousand dollars ($1,000), must be in writing with a copy of the contract provided to the customer, unless otherwise directed by the customer.
6.6General Licensing of Well-Drillers, Pump Installers, Water Filtration Contractors and Water Filtration Installers Requirements
A.The licensing of well-drillers, pump installers, water filtration contractors, and water filtration installers shall comply with R.I. Gen. Laws Chapters § 5-65, 5-65.2, and the following sections of Part 1 of this Subchapter:
1.Registration Required: § 1.6.1 of this Subchapter.
2.Transference of Registration Prohibited: § 1.6.2 of this Subchapter.
3.Display of Registration Number: § 1.6.3 of this Subchapter.
4.Business Entity Registrations: § 1.6.4 of this Subchapter.
5. Nonresident Persons / Registered Agent: § 1.6.5 of this Subchapter.
6.Change of Registration: § 1.6.6 of this Subchapter.
7.Effect on Registration Due to Loss of Responsible Person: § 1.6.7 of this Subchapter.
B.Pursuant to R.I. Gen. Laws § 5.65.2-3, upon satisfaction of all licensing requirements and the payment of a separate fee for each, the Board is authorized to issue the following licenses:
1.Well-drilling contractor;
2.Pump installer;
3.Water-filtration/treatment-system contractor, and/or
4.Water-filtration/treatment-system installers.
C.As a condition of licensure, all well drilling contractors, pump installers, water filtration/treatment-system contractors, and water filtration/treatment installers who are licensed with the Board, shall participate and make good faith efforts to resolve all complaints, violations, and/or contested cases within the jurisdiction of the Board. Failure to do so shall result in the Board taking action against the well drilling contractor, pump installer, water filtration/treatment-system contractor, or water filtration/treatment installer to the extent allowable by law, including suspension of a well drilling contractor, pump installer, water filtration/treatment-system contractor, or water filtration/treatment installer’s license, without which a well drilling contractor, pump installer, water filtration/treatment-system contractor, or water filtration/treatment installer cannot perform work in the State of Rhode Island.
D.Exemption
1.Any water authority regulated by the R.I. Department of Health engaged in well drilling shall be exempt from the registration and/or license provisions of R.I. General Law Chapters 5-65 and 5-65.2 so long as the work is done by regular employees of, and with equipment owned by, the water authority, and the work is on wells intended for use by the water authority.
E.Grace Period: Compliance with the requirements of this Part shall begin as of the date this Part goes into effect. Enforcement of the licensing requirements shall begin on April 1, 2020.
6.7Applications for Licensure
A.Applications for the licensure of well-drillers, pump installers, water filtration contractors, and water filtration installers shall comply with R.I. Gen. Laws Chapters 5-65, 5-65.2, and the following sections of Part 1 of this Subchapter:
1.General Application: § 1.7.1 of this Subchapter.
2.Examination: § 1.7.2 of this Subchapter.
3.Effective Date / Term: § 1.7.3 of this Subchapter.
4.Renewal and Reissuance of Registration: § 1.7.4 of this Subchapter.
5. Lapsed Registration: § 1.7.5 of this Subchapter.
6.Military Service Registration: § 1.7.6 of this Subchapter.
B.Grandfather Clause
1.Prior to April 1, 2020, the Board shall, without examination, upon receipt of the fees required in this chapter, issue a residential water-filtration/treatment-system installer's license to any applicant who shall present satisfactory evidence that they have the qualifications for the type of license applied for. After April 1, 2020, in order to qualify for a residential water-filtration/treatment installer's license the eligible individual shall be required to pass a written examination and show proof as required by the contractors' registration and licensing board of their eligibility.
a.Satisfactory evidence shall be any of the following that is applicable:
(1)The applicant must have been employed by a contractor registered with the contractors' registration and licensing board to do business designating water-filtration/treatment-system installation and/or service as a service provided for the previous one year and been actively engaged in the installation and servicing of water-filtration/treatment systems during that time period; or
(2)Notarized confirmation by three (3) water-filtration/treatment-system contractors that the applicant has the requisite training and experience to be licensed under this act.
2.Prior to April 1, 2020, the Board shall, without examination, upon receipt of the fees required in this chapter, issue a residential water-filtration/treatment-system contractor's license to any applicant who shall present satisfactory evidence that they have the qualifications for the type of license applied for. After April1, 2020, in order to qualify for a residential water-filtration/treatment contractor's license, the eligible contractor shall be required to pass a written examination and show proof, as required by the contractors' registration and licensing board, of their eligibility.
a.Satisfactory evidence shall be any of the following that is applicable:
(1)The owner or owners of an enterprise must have been active in water filtration for the previous two (2) years; or
(2)The contractor has been previously registered with the contractors' registration and licensing board to do business designating water-filtration/treatment system installation and/or service as a provided service; or
(3)Notarized confirmation by three (3) water-filtration/treatment-system contractors that the applicant has the requisite training and experience to be licensed under this act.
3.Those well-drilling contractors who were previously registered with the department of environmental management, and remain in good standing as of December 31, 2019, and that were previously exempted from fulfilling the testing requirements required for registration by the department, shall also be exempt from the testing requirements set forth in this chapter.
6.8Education Requirements - Pre-Registration and Continuing Education
A.Educational requirements for the licensing of well-drillers, pump installers, water filtration contractors, and water filtration installers shall comply with R.I. Gen. Laws Chapters 5-65, 5-65.2, and the following sections of Part 1 of this Subchapter:
1.Scope: § 1.8.1 of this Subchapter.
2.Specifications: § 1.8.2 of this Subchapter.
3.Qualifying Education: § 1.8.3 of this Subchapter.
4.Course Materials and Fees: § 1.8.4 of this Subchapter.
5. Proof of Educational Course Completion / Compliance: § 1.8.5 of this Subchapter.
6.Educational Requirements: § 1.8.6 of this Subchapter.
7.Exception to Educational Requirements: § 1.8.7 of this Subchapter.
8. Violations for Failing to Complete Educational Requirements: § 1.8.8 of this Subchapter.
9.Educational Course Providers § 1.8.9 of this Subchapter.
10.Educational Courses § 1.8.10 of this Subchapter.
11. Violations for Operating as a Non-Approved Provider: § 1.8.11 of this Subchapter.
12.Penalties for Provider Noncompliance: § 1.8.12 of this Subchapter.
B.Continuing Education Required for License Renewal.
1.As a condition of a license renewal, well-drillers, pump installers, water filtration contractors, and water filtration installers shall complete ten (10) hours of Board approved continuing education courses with a Board approved provider during each two (2) year license period. These courses must be related to the practices of well-drillers, pump installers, water filtration contractors, and water filtration installers. or other topics related to the nature of the licensee's business.
2.Each licensee shall maintain documentation for all continuing education for three (3) license cycles and shall furnish this documentation to the Board upon request.
6.9Complaints
A.The procedure for filing a complaint against a home inspector or associate home inspector shall comply with R.I. Gen. Laws Chapters 5-65, 5-65.2, and the following sections of Part 1 of this Subchapter:
1.Duty to Participate: § 1.9.1 of this Subchapter.
2.Complaints Generally: § 1.9.2 of this Subchapter.
3.Board Initiated Investigations: § 1.9.3 of this Subchapter.
4.The Board's Right to Refuse and/or Dismiss Complaints: § 1.9.4 of this Subchapter.
6.10 Notice of Accepted Complaints and Initial Board Investigation
The rules and regulations for pertaining to the notice of accepted complaints and initial board investigation shall comply with R.I. Gen. Laws Chapters § 5-65, 5-65.2, and § 1.10 of Part 1 of this Subchapter:
6.11Prehearing Conferences and Alternative Dispute Resolution
A.The rules pertaining to prehearing conferences and alternative dispute resolution shall comply with R.I. Gen. Laws Chapter 5-65 and the following sections of Part 1 of this Subchapter:
1.Pre-Hearing Conferences: § 1.11.1 of this Subchapter.
2.Alternative Dispute Resolution: § 1.11.2 of this Subchapter.
3.Pre-Hearing/Alternative Dispute Resolution Procedures: § 1.11.3 of this Subchapter.
4.Administrative Hearings Based on Contested Cases: § 1.11.4 of this Subchapter.
6.12Violations
A.The rules pertaining to violations shall comply with R.I. Gen. Laws § 5-65 and the following sections of Part 1 of this Subchapter:
1.Authority: § 1.12.1 of this Subchapter.
2.Procedure for Investigating and Processing Violations: § 1.12.2 of this Subchapter.
3.Notices of Violation/Proposed Order: § 1.12.3 of this Subchapter.
4.Fines / Penalties: § 1.12.4 of this Subchapter.
5.Court Judgments/Arbitration Awards - Effect on Registration/License: § 1.12.5 of this Subchapter.
6.13Appeals
A.The rules pertaining to appeals shall comply with R.I. Gen. Laws Chapter 5-65 and the following sections of Part 1 of this Subchapter:
1.Appeal of Notice of Violation to Hearing Officer: § 1.13.1 of this Subchapter.
2.Appeal of Final Order by the Hearing Officer to the Full Board: § 1.13.2 of this Subchapter.
3.Appeal of Final Order by the Full Board to the Superior Court: § 1.13.3 of this Subchapter.
6.14Criminal Prosecution
The rules pertaining to criminal prosecution shall comply with R.I. Gen. Laws Chapter 5-65 and § 1.14 of this Subchapter.
6.15 Administrative Hearings
A.The rules pertaining to administrative hearings shall comply with R.I. Gen. Laws Chapters 42-35 and 5-65 and the following sections of Part 1 of this Subchapter:
1.Notice of Hearing: § 1.15.1 of this Subchapter.
2.Representation: § 1.15.2 of this Subchapter.
3.Filing of Pleadings and Other Documents: § 1.15.3 of this Subchapter.
4.Service: § 1.15.4 of this Subchapter.
5.Time: § 1.15.5 of this Subchapter.
6.Motions: § 1.15.6 of this Subchapter.
7.Discovery: § 1.15.7 of this Subchapter.
8.Subpoenas: § 1.15.8 of this Subchapter.
9.Evidence: § 1.15.9 of this Subchapter.
10.Conduct of Hearings: § 1.15.10 of this Subchapter.
11.Decisions: § 1.15.11 of this Subchapter.
6.16Expungements
The rules pertaining to expungements shall comply with R.I. Gen. Laws Chapter 5-65 and § 1.16 of this Subchapter.
6.17Default
The rules pertaining to default shall comply with R.I. Gen. Laws Chapter 5-65 and § 1.17 of this Subchapter.
6.18Disqualification/Incapacity of Hearing Officer
The rules pertaining to disqualification / incapacity of Hearing Officer shall comply with § 1.18 of this Subchapter.
6.19Miscellaneous Provisions
The rules pertaining to miscellaneous provisions shall comply with § 1.19 of this Subchapter.
6.20 Hearings - Public Information
The rules pertaining to the hearings - public information shall comply with § 1.20 of this Subchapter.
6.21Publication of Orders and Notices
The publication of all orders issued by the board and notices of hearing shall comply with the requirements of R.I. Gen. Laws § 5-65-25.
6.22Equal Access to Justice for Small Business
The rules pertaining to the equal access to justice for small business shall comply with § 1.22 of this Subchapter.
6.23Severability
The rules pertaining to severability shall comply with § 1.23 of this Subchapter.
6.24Performance Standards
A.The performance standards are intended to specify the minimum performance standards and requirements for the construction, alteration, installation, and repair of wells and pumps, and residential filtration/water treatment systems. Supplemental performance standards for wells, pumps and filtration/water treatment for public water systems, as described in R.I. Gen. Laws Chapter 46-13, can be found in 216-RICR-50-05-1.
B.Well-drillers, pump installers, water filtration contractors, and water filtration installers shall perform all work in accordance with R.I. Gen. Laws Chapters 5-65 and 5-65.2, these Rules and Regulations, any plans and specifications governing the project(s), and city/town/municipal regulations.
C.The Board’s investigators and/or staff may inspect well-drillers, pump installers, water filtration contractors, and water filtration installers work to ensure it complies with all applicable laws, regulations, city/town/municipal regulations, plans, and specifications governing the project, industry standards, manufacturers' specifications. Contractor responsibility may not extend to items which have been subject to owner neglect, modifications, or abnormal use.
6.24.2Defects in Equipment
Nothing in this Part creates a warranty or limitations on a warranty for defective equipment.
6.24.3Applicable Building Code
A.For the purposes of this Part, the building code governing the life safety, structural, mechanical, plumbing, electrical, fuel, gas, and energy requirements for well drillers, pump installers, and water-filtration/treatment-system work shall be the building code that was adopted and in effect at the time the work was completed.
B.Well drillers, pump installers, and water-filtration/treatment system contractors and installers must also comply with 216-RICR-50-05-1 when working on public water systems as defined in R.I. Gen. Law § 46-13-2.
6.24.4Filtration and Treatment of Water
All installations and/or repairs shall meet or exceed all applicable State building codes, and Water Quality Association, and National Sanitation Foundation/American National Standards Institute standards.
6.24.5 Construction Standards for Public Water Wells
In addition to the applicable standards found in this Part, standards for public water systems, including wells, pumps, filtration/treatment and other appurtenances are set forth by the Rhode Island Department of Health in 216-RICR-50-05-1.
6.24.6 Construction Standards for Non-Public Water Wells
A.Well Location Wells shall be located in a manner to reduce the likelihood of contamination from sources of pollution at or near the ground surface.
1.The following are minimum isolation distances from the listed potential contamination sources:
Distribution Box | 75 feet |
Septic Tank | 75 feet |
Sewage Disposal Field, including cesspools | 100 feet |
Sewer Line | 50 feet |
Road | 25 feet from the edge of the road surface |
Fuel Storage Tanks | As far as possible from wells |
Livestock Pens / animal waste storage facility | No well shall be located within 100 feet |
Active Agricultural Areas | Minimum of 20 feet and uphill whenever possible |
2.Tiered Separation Distances between leach field and private wells based on OWTS Design Flow:
Design Flow (gpd) | Distance from Leach field (ft) |
<1000 | 100 |
1000-1999 | 150 |
2000-4999 | 200 |
5000-9999 | 300 |
3.Source of Contamination Additional Distance Requirements
Agricultural chemical: |
|
tank or container with 25 gallons or more or 100 pounds or more dry weight, or equipment filling or cleaning area without safeguards | 150 feet |
storage or equipment filling or cleaning area with safeguards | 100 feet |
storage or equipment filling or cleaning area with safeguards and roofed | 50 feet |
Anhydrous ammonia tank | 50 feet |
Animal: |
|
feedlot, unroofed, 300 or more animal units | 100 feet |
feedlot, more than 1.0, but less than 300 animal units | 50 feet |
building or poultry building, including a horse riding area, more than 1.0 animal unit | 50 feet |
Rendering plant | 100 feet |
feeding or watering area within a pasture, more than 1.0 animal unit | 50 feet |
area to bury more than one animal unit | 100 feet |
building, feedlot, confinement area, or kennel, 0.1 to 1.0 animal unit | 20 feet |
Building, building projection, deck, overhang, permanent structure | 3 feet |
Cistern or reservoir, buried, non-pressurized water supply | 20 feet |
Composting |
|
Leaf and yard waste | 200 feet |
Putrescible waste | 200 feet |
Mixed Solid Waste | 1000 feet |
Construction or demolition debris disposal area | 500 feet |
Cooling water pond, industrial | 50 feet |
Deicing chemicals, bulk road | 50 feet |
Drain field (see Absorption area) |
|
Electric transmission line | 10 feet |
Electrical transformer storage area, oil-filled | 50 feet |
Elevator boring, not conforming to rule | 50 feet |
Elevator boring, conforming to rule | 20 feet |
Fertilizer chemigation tank, safeguarded, from irrigation well only | 20 feet |
Floor drain, grate, or trough connected to a buried sewer | 50 feet |
if buried sewer is air-tested, approved materials, serving one building, or two or less single-family residences | 20 feet |
Frost-proof yard hydrant or discharge of a frost-proof hydrant draining into the soil, fire hydrant or flushing hydrant | 10 feet |
Gas (flammable or volatile) pipe | 10 feet |
Grave or mausoleum | 50 feet |
Human Remains | 100 feet |
Gravel pocket or French drain for clear water drainage | 20 feet |
Hazardous substance: |
|
tank or container, above ground or underground, 56 gallons or more, or 100 pounds or more dry weight, without safeguards | 150 feet |
tank or container, above ground or underground, 56 gallons or more, or 100 pounds or more dry weight with safeguards | 100 feet |
Buried piping: | 50 feet |
multiple storage tanks or containers for residential retail sale or use, no single tank or container exceeding 56 gallons or 100 pounds, but aggregate volume exceeding | 50 feet |
Horizontal ground source closed loop heat exchanger buried piping | 50 feet |
Horizontal ground source closed loop heat exchanger buried piping and horizontal piping, approved materials, and heat transfer fluid | 10 feet |
Household solid waste disposal area, single residence | 100 feet |
Interceptor, including a flammable waste or sediment | 50 feet |
Petroleum | 300 feet |
Unused, unsealed well or boring | 50 feet |
Vertical heat exchanger (vertical) piping, conforming to rule | 35 feet |
horizontal piping conforming to rule | 10 feet |
Wastewater rapid infiltration basin, municipal or industrial | 300 feet |
Wastewater spray irrigation area, municipal or industrial | 150 feet |
Wastewater stabilization pond municipal, 500 or more gallons/acre/day of leakage | 300 feet |
municipal, less than 500 gallons/acre/day of leakage | 150 feet |
industrial | 150 feet |
Wastewater treatment unit tanks, vessels, and components (Package plant) | 50 feet |
Water treatment backwash disposal area | 50 feet |
Water treatment backwash holding basin, reclaim basin, or surge tank with a direct sewer connection | 50 feet |
with a backflow protected sewer connection | 50 feet |
Stormwater Infiltration System, distances pursuant to 250-RICR-150-10-8 |
|
3.The well driller shall inform the property owner of the proper isolation distances from pollution sources. The property owner shall provide information to the well driller on the location of existing reserved and permitted areas for subsurface disposal fields and other pollution sources. If the property owner is unable to provide such information, the property owner shall obtain that information from the city/town hall or the Onsite Wastewater Treatment Systems (OWTS) Section of the Department of Environmental Management.
B.Variances
1.In those circumstances in which compliance with the requirements for locating a new or replacement non-public water well would result in undue hardship, property owners may seek a variance from any one or more of the siting requirements, in accordance with the following:
a.Except as specified in (c), from the building code board of appeals authorized in the municipality with jurisdiction over the property on which the well is proposed;
b.Except as specified in (c), in the absence of a local building code board of appeals, from the state building code board of appeals; and
c.From the Department of Environmental Management in all cases in which the well is proposed to be installed as part of an application for the new construction of or repair of an onsite wastewater treatment system. The appropriate authority specified above may grant a variance to the extent necessary to ameliorate the undue hardship and to the extent the exemption can be granted without impairing the intent and purpose of this chapter.
C.General Requirements for New Non-Public/Private Systems
1.Prior to being placed into service, the local building official shall verify that all new private water systems or existing private water systems meet all applicable codes and standards.
2.As specified in the rules and regulations for Private Drinking Water Systems (216-RICR-50-05-2), all required testing shall be performed after all plumbing and water-using appliances are in place and the system has been properly disinfected in accordance with § 6.24.17 of this Part. The sampling point for this sample shall be an interior faucet that yields untreated (raw) well water. Testing must be conducted prior to the installation of any drinking water quality treatment systems. All drinking water quality treatment systems in-place shall be identified and noted.
3.All water samples for lead analyses shall be acquired as first draw samples from the cold-water tap. Bubblers or drinking fountains shall not be satisfactory sampling points. All treatment systems in-place shall be identified and noted.
D.Basic Restrictions
1.All water used in the construction, alteration, repair, hydro fracturing, surging or abandonment of a well shall be drawn from a potable source.
2.Organic materials which foster or promote undesired organic growth or have the potential to degrade water quality shall not be employed in the construction of a drinking water well. This includes but is not limited to brans, hulls, grains, starches, and proteins.
3.In no case shall explosives be detonated inside the well casing or liner pipe without written permission from the Rhode Island State Fire Marshall. The request shall include the type of explosive to be used and how they will be placed. In no case shall an explosive charge be dropped down a well or used to sever installed well casing or liner pipe.
4.System piping installed for geothermal wells shall not extend more than five (5) feet into a structure to a shutoff.
5.No well shall be used for the injection of surface water.
6.In no case shall a well be constructed to allow commingling or leakage of groundwater within an individual well by gravity flow or artesian pressure from different groundwater aquifers associated with different geological units.
7.All wells that yield contaminated or mineralized water, and therefore are not usable, must be adequately cased and sealed off to prevent contamination of the overlying or underlying water-bearing zones.
8.All wells when unattended during construction must be secured per recognized industry standards.
E.Drilling - General
1.The well driller shall not cause undue soil erosion or water pollution and shall not pollute the site with fuels, lubricants, solvents, or other contaminants used in construction of the well. Any drilling fluids used shall be disposed of properly.
2.The well driller shall use care in the selection and use of drilling fluids, additives, cements, and other materials to avoid materials and procedures that may adversely affect the drill site, or any groundwater encountered. Any chemical or other additives used in drilling along with rock cuttings shall be cleaned out from the well.
3.Well drillers drilling a well for potable water shall not reuse casing or drilling fluids that may have become contaminated. All drilling equipment that may have become contaminated during a drilling operation shall be thoroughly cleaned, decontaminated, and disinfected before reuse.
4.Disinfection shall be as per § 6.22.19 of this Part.
5.Wells shall be designed to be of adequate diameter and depth capable of yielding the quantity of water required by appendix B of these standards.
F.Pumps and Pumping Equipment
1.Pumps and pumping equipment shall be installed to make the most efficient use of well.
2.Pumps and pumping equipment shall be located to permit convenient access for inspection, maintenance, and repair.
3.In the event the base plate of a pump is placed directly over the well, the base plate shall be a type designed to form a water tight seal with the well casing or pump foundation.
4.The well shall be properly vented to allow for pressure changes within the well. It shall also be fitted with a pitless adaptor. All well covers must have sanitary seals.
5.Potable water must be used for priming all pumps.
6.The electrical wiring used in connection with the pump shall conform to the current specifications of the Rhode State Electrical Code (SBC-5).
7.The pump installer shall disinfect a well subsequent to installation of a pump to the standards.
6.24.7Standards for Wells in Unconsolidated Materials
A.Any well, constructed to obtain water from an unconsolidated rock formation shall be equipped with a screen, for the purpose of preventing the entrance of formation material into the well after the well has been developed and completed.
B.The well screen shall:
1.Be of a standard design and manufacture, for the specific purpose of well construction;
2.Be made of material adequate to withstand normal physical and chemical forces, applied to it during and after installation;
3.Have openings free of rough edges, irregularities, or other defects that may contribute to corrosion or clogging; and
4.Be provided with such fittings as are necessary to seal the top of the screen to the casing and to close the bottom, and in no case shall fittings be made of lead.
C.Any well, constructed in very coarse gravel largely free of fines, shall not, however, be required to have a screen; or, if a screen is used, the bottom may be left open.
D.Jetted or washed wells shall not be terminated in unconsolidated materials unless an adequate quantity of water free from fine soil particles can be withdrawn.
E.To allow for grouting, unconsolidated wells shall have an upper drill hole 3" or 4" greater in diameter than the nominal diameter of the permanent well casing, depending on the type of grout.
F.In all cases, cases a minimum of 18 feet of casing and casing seal will be required.
6.24.8 Standards for Artesian Wells
A.To allow for grouting, unconsolidated wells shall have an upper drill hole 3" or 4" greater in diameter than the nominal diameter of the permanent well casing, depending on the type of grout
B.Watertight unperforated casing shall extend and be sealed at least 5' into the confining formation immediately overlying the artesian water-bearing zone.
C.In all cases a minimum of 18 feet of casing and casing seal will be required.
D.If a well flows at the land surface, the well shall be equipped with a watertight mechanical cap, threaded or welded, and a control valve, so that all flow of water from the well can be completely stopped.
E.All flowing artesian wells shall be tested for artesian shut-in pressure in (psi) and rate of flow in ft/sec., or gal/min. under free discharge conditions. This data shall be reported on the well report.
6.24.9 Standards for Drilled Rock Wells
A.To allow for grouting, drilled rock wells shall have an upper drill hole 3" or 4" greater in diameter than the nominal diameter of the permanent well casing, depending on the type of grout.
B.The bottom of the casing shall be set securely into the rock in a manner which is adequate to prevent fluids, contaminations, or rock material from the ground surface or from any zone from entering the well.
C.All wells drilled into bedrock shall be completed with water tight casing and casing seal to a minimum depth of 18 feet below the land surface and no less than 5 feet into the bedrock.
D.A drive shoe may be used to assist in sealing the casing into bedrock.
E.When plastic casing is used, the seal shall be created by the use of a Jaswell-type seal tip, shale packer or equal.
F.When a well is re-cased for the purpose of shutting off undesirable water or sand, a Jaswell-type seal tip shall be used, and the annular space be grouted with an acceptable material.
G.A tapered hole to receive the outer diameter of the plain end casing is acceptable.
H.When bedrock is encountered within 10 feet, air may be used to lift the cuttings from the bore hole. However, when the depth to bedrock is greater the cuttings must be removed by slurries mudding method which will then insure the annular space to be free from voids to allow for proper grouting.
6.24.10 Construction of Shallow Wells in Unconsolidated Materials by Excavation (Dug Wells)
A.Dug wells are prohibited for new private and public drinking water systems but are permissible for other uses.
1.For situations where no other alternatives exist and such prohibition would be the sole factor in rendering the subject property non-buildable, application may be made to the Board for a variance to allow a dug well to be utilized as a private drinking water source.
B.The following standards pertain to repairs to existing dug wells that can be repaired to the extent required to maintain source potability.
1.Upper joints in well casings shall be sealed to exclude surface and near surface water from entering the well.
2.The bottom of the casing shall be set on a bed of clean crushed stone or naturally occurring coarse gravel, if present.
3.Crushed stone shall be placed around the exterior of the casing at the bottom section(s) to promote infiltration of water and provide additional storage, if appropriate for the soil conditions at the site.
4.Backfill shall be of an appropriate material and placed in a manner which will deter intrusion of soil into the well and reduce the likelihood of surface waters percolating directly into the well through the backfill.
5.Organic material shall not be used in the backfill including but not limited to: loam, peat, building paper, hay, or soil with organic matter.
6.Pea stone or other non-polluting barriers shall be used over the crushed stone to prevent fine soils from entering the crushed stone.
7.Backfill shall be compacted to reduce settlement.
8.The top of the backfill shall be covered with at least 2 feet of impervious material such as clay.
9.The ground surface at the well should be raised and graded to drain away from the well taking into consideration future settlement of the backfill.
10.The dug well shall be provided with a watertight cover constructed of a single integral material so as to prevent sources of contaminants from entering the well.
6.24.11 Casing
A.The casing material used on all water wells shall be of such strength and composition as to prevent the movement of water or contaminants into or out of the well in the interval so cased; and shall not distort, deform, collapse, crack, or disintegrate under normal conditions for the life of the well, or contaminate the water in the well.
B.The casing shall be adequate to provide for the installation, removal, and maintenance as appropriate of caps, pitless adaptors, screens, pumps, pipes, wires, or other devices which may be used throughout the normal life of the well.
C.Casing shall prevent intrusion of contaminants from the ground surface or unconsolidated soil layers into the well.
D.Steel well casing shall have a minimum wall thickness of 0.237 inches for wells drilled in bedrock and deep wells in unconsolidated materials.
E.Well casings shall have an airtight cover with a sanitary seal, and a screened vent to prevent the entrance of foreign matter into the well.
F.Well casing shall extend above the ground surface a minimum of 18 inches. In areas prone to flooding, additional casing heights must be installed to prevent entrance of surface water. Wells that serve public water system must adhere to the requirements of 216-RICR-50-05-1.
G.The above requirements do not preclude the use of additional protection measures.
6.24.12 Grouting annular space
A.Public Wells: Well grouting for all public drinking water wells shall be in accordance with 216-RICR-50-05-1.
B.Private Wells: Well grouting for all private drinking water wells may be accomplished as follows:
1.In cases where no more stringent standards are required, and there is no evidence of existing or potential contamination sources or excessively corrosive condition and the natural materials contain a significant proportion of naturally impervious materials mixed with drilling mud, the driller may fill the annular space with the natural materials excavated during the drilling of the well to meet the following requirements:
a.The annular space shall be fitted as completely as possible from the bottom or the casing to the land surface without any depressions, voids, holes or channels;
b.The driller shall employ whatever techniques are effective for the existing conditions to achieve maximum density, strength and impermeability of the fill material; and
c.The surface of the fill material shall be sloped away from the casing.
2.In cases where potentially contaminating or corrosive fluids are encountered, or impermeable natural materials cannot be adequately placed and compacted or where geologic conditions or the isolation distance may not be adequate, the annular space shall be grouted for the full length of the casing, or the portion thereof below the frost line or pitless adaptor, so that no fluids may move in the zone needing to be grouted.
3.In cases where frost heaving is likely, the annular space from the frost line to the ground surface may be filled with compacted granular fill to reduce the potential for frost heaving of the casing. The casing shall be securely supported by the surrounding fill material to a degree that it cannot be moved by manual means.
4.In no case will a driller leave a completed well with water flowing or standing in the annular space.
6.24.13 Maintenance, Repair, and Deepening of Wells
A.Valves and casing on all artesian wells shall be maintained in a condition so that the flow of water can be completely stopped when the water is not being put to beneficial use. All casing, liner pipe, and casing seals shall be maintained in a condition that will prevent surface or subsurface leakage of groundwater. Valves shall be closed when water is not being put to beneficial use. During period of subfreezing temperatures, care shall be taken to prevent damage due to freezing. The pressure gauge and petcock valve shall be maintained so that the artesian pressure can be accurately determined at any time.
B.If in repair of a drilled well the old casing is withdrawn, the well shall be re-cased and resealed.
C.The access port or airline on all wells shall be maintained in a condition that will prevent contamination of the water body. Access ports and air lines shall be maintained so that the position of the water table can be determined at any time.
D.In no case shall a dug well be deepened, unless the deepening is for the purpose of developing a bedrock or gravel packed drilled well. This is allowed only if the siting requirements listed in § 6.22.6 of this Part preclude the development of a drilled well elsewhere on the property.
6.24.14 Temporary Removal from Service
Any well to be temporarily removed from service, either due to a recess in construction or before commencing service, shall be capped with a watertight seal, watertight welded steel cap, or threaded cap. In the event that temporary removal from service is to be more than 90 days or more, the temporary steel cap must be welded to the well casing with a minimum of four (4) separate welds, evenly spaced, each at least 1/2 of an inch in length. Steel or cast-iron caps shall be at least 3/16 of an inch in thickness.
6.24.15 Decommissioning of Wells:
A.Abandoned wells, test wells and bores must be decommissioned.
B.Decommissioning of all potable water wells and potable test wells and bores associated with a private well shall be in accordance with 216-RICR-50-05-1 and the following:
1.The well shall be disinfected prior to decommissioning in accordance with§ 6.22.18 of this Part.
2.All casing and screen materials that have salvage value may be removed by the contractor.
3.Upon completion of abandonment of the well, the top of the casing or grout material shall be terminated at least four (4) feet below the ground surface.
C.Decommissioning of ground water monitoring wells, piezometers, and others subsurface borings shall be done in compliance with 250-RICR-150-05-03.
D.Decommissioning of a geothermal well shall be performed only by a licensed well driller.
6.24.16 Record of Wells
Within ten (10) days after completion of a new, reconstructed, replacement or decommissioned well, whether attached to an existing building or planned building, the licensed well contractor shall provide the owner, the Building Official and the Department of Health, a Well Completion Report on a form obtained from the Department of Health, completed in its entirety in accordance with R.I. Gen. Laws § 46-13.2-5.
6.24.17 Electrical/Plumbing
Any licensed person or entity under these regulations may perform electrical and/or plumbing work as defined in the definitions of Rhode Island General Law 5-65.2-2 in relation to the work performed pursuant to these regulations and R.I. General Law. Nothing herein shall prohibit any Rhode Island licensed electrician or plumber from performing similar work. All electrical or plumbing work performed shall meet the State of Rhode Island; electrical code (SBC-5) and plumbing code (SBC-3).
6.24.18 Disinfecting
Disinfecting shall be accomplished in accordance with the Rhode Island Department of Health well disinfection guidelines.
6.24.19 Drilling Depths
A.For the use of individual household, bedrock well of 6 inches in diameter shall be satisfactory when it meets the following minimum criteria:
1.With a yield of 5 gpm, a minimum depth of 100' or less is required.
2.With a yield of 3 1/2 gpm, a minimum depth of 150' is required.
3.With a yield of 2 gpm, a minimum depth of 200' is required.
4.With a yield of 1 gpm, a minimum depth of 300' is required.
5.With a yield of 1/2 gpm, a minimum depth of 450' is required.
B.This is assumed that the static water level is between 25 and 35 feet and the pump has been appropriately set to insure maximum productivity. The above is intended as a construction standard and does not imply or guarantee actual yield.
C.Special caution should be exercised in coastal areas because of potential saltwater intrusion.
Title | 440 | Contractors' Registration & Licensing Board |
Chapter | 10 | General Administration, Registration, Licensing, and Filing Claims |
Subchapter | 00 | N/A |
Part | 6 | Rules and Regulations for Well-Drillers, Pump Installers, and Water Filtration Contractors |
Type of Filing | Periodic Refile |
Regulation Status | Active |
Effective | 01/04/2022 |
Regulation Authority:
R.I. Gen. Laws § 5-65.2-3(d)
Purpose and Reason:
This rule is being refiled by the agency pursuant to R.I. Gen. Laws § 42-35-4.1. No changes were made to the text of this rule.
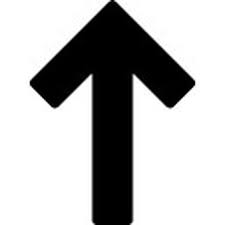
Rulemaking Documents are organized by document type and are part of this rule’s rulemaking record (R.I. Gen. Laws § 42-35-2.3). If multiple documents of the same type are listed below, each is a unique document. If there are multiple Public Notice of Proposed Rulemaking documents, view each document to identify the most recently amended version, as it may be amended at any point during the Public Comment Period.